Introduction
Work order management is the most important feature of ServiceMax. If the customers raise any issues regarding the products installed at a particular location, the work order management helps the technicians to document the information of the complete work order with minimal disruption to clients. The technician can generate a document with all the information related to work order after completion of the work order. ServiceMax is one of the leading field service management solutions, it excels in this area by offering clients robust work order management. In this post, we’ll discuss how ServiceMax simplifies work order administration and provide an actual case study to show how it works.
The ServiceMax Approach to Work Order Management
Work order management in ServiceMax begins with a service request, typically generated when a customer reports an issue with an installed product (If a product is installed at a particular location then it is called as an installed product).
For instance, imagine a large telecommunications company that uses ServiceMax to manage its field operations across multiple regions in India.
A customer in the North region reports that their communication equipment is malfunctioning. If the issue can be resolved over the phone then the service request will be closed. However, if further action is needed, a work order is created from this request.
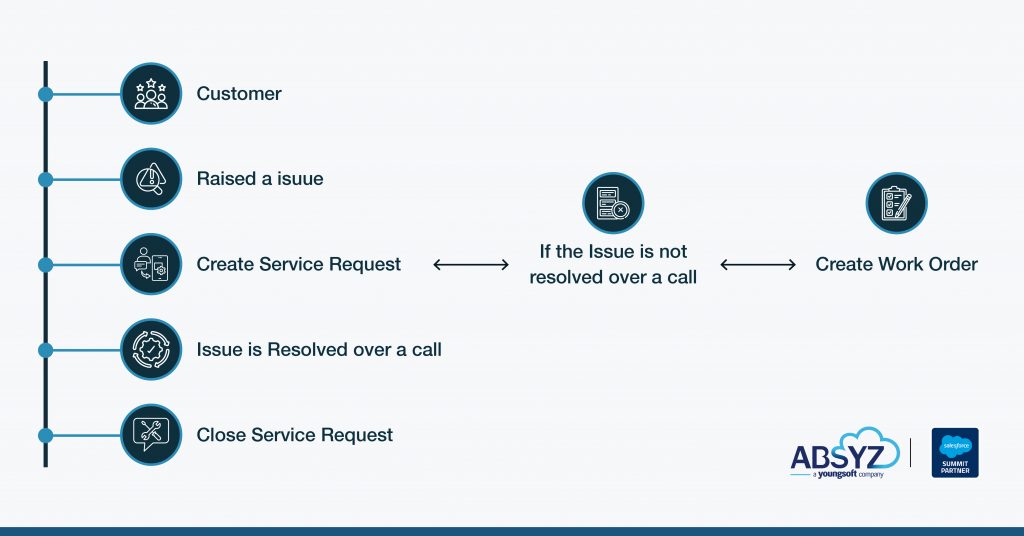
This work order includes critical details such as:
Customer Information: Account, Contact details and service history.
Equipment Details: The specific product involved, including its serial number and warranty status.
Location: Where the equipment is located.
Task Requirements: The steps that need to be taken to resolve the issue.
Assignment and Dispatching
The telecoms corporation in our case has divided its service teams into four regional service territories: North, East, West, and South.
A professional dispatcher for each territory uses the ServiceMax dispatch console/service board to assign work orders to technicians according to their availability, location, and skill set.
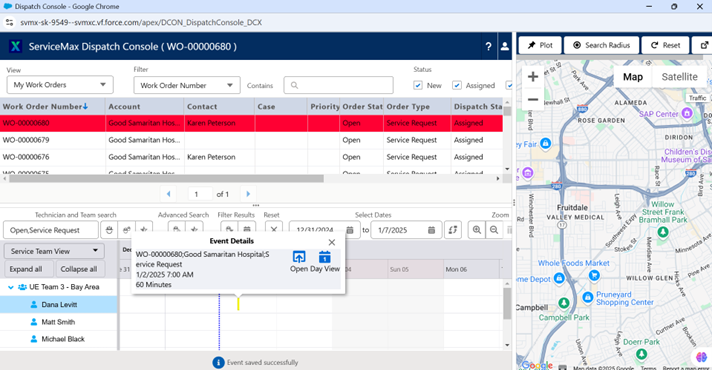
The dispatcher chooses a professional who specializes in communication systems and is nearest to the customer’s location for the reported equipment issue in the North area.
The work order with all the information will be assigned to the technician by the dispatcher. The technician will receive a work order notification on the Go App with all necessary details to prepare for the job.
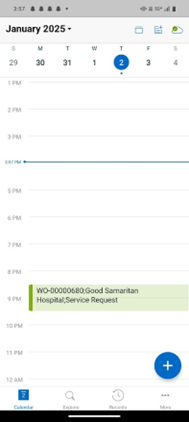
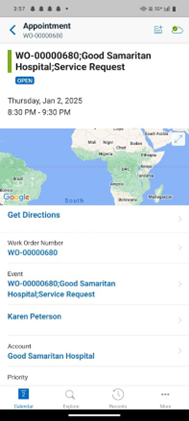
Customizable Work Orders for Different Scenarios
ServiceMax offers the flexibility to create different types of work orders, each tailored to specific tasks. Let’s expand on our example:
Repair Work Order: If the equipment malfunctions, the work order will include the procedures for identifying and fixing the problem. Every stage of the process is walked through with the technician, from troubleshooting to testing the equipment once repairs are finished.
Preventive Maintenance Work Order: ServiceMax allows the company to set up preventive maintenance (PM) plans for scheduling the maintenance of the products. These plans automatically generate work orders at specified intervals based on the requirements, ensuring that equipment receives timely servicing, and reducing the risk of future breakdowns.
Installation Work Order: If the customer requires new equipment installation at a particular location then this type of work order can be used.
Decommission Work Order: If the customer wants to remove the equipment from a particular location, then a decommission work order can be used.
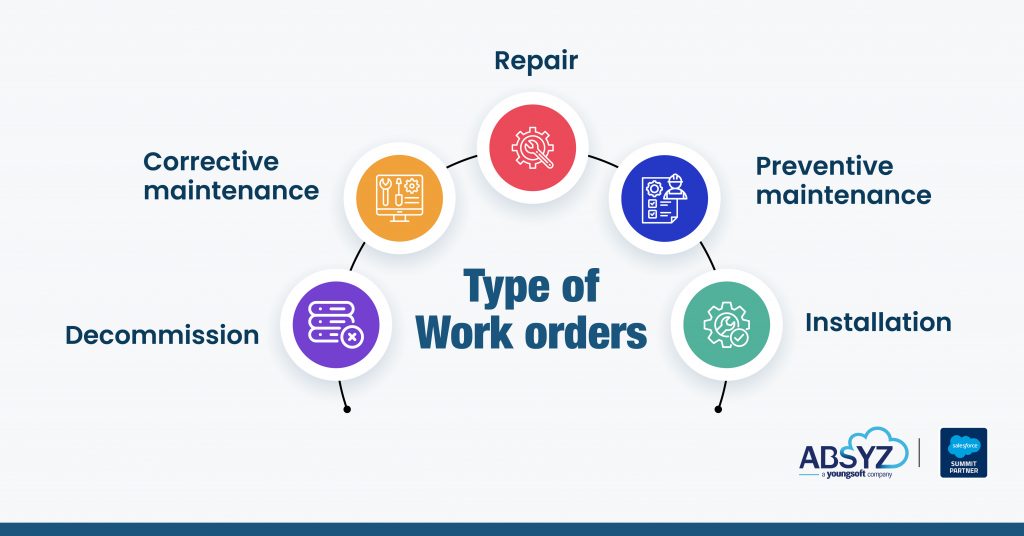
Managing Parts and Logistics
Effective parts management is crucial for minimizing downtime. In our example, the technician may need a specific part to repair the communication equipment. ServiceMax allows the dispatcher to order the required parts, ensuring they are delivered to the technician’s location before the scheduled repair. If any parts are defective, the system handles returns and reorders seamlessly, preventing delays.
Closing the Work Order
After completing the task, the technician checks that the equipment is functioning properly. After that, the technician can generate a document which includes all the information about the parts used, the time spent, and any new observations added in the work order. This document can be shared with the client and the back office which includes all the information and helps for the accurate billing. After completion of all the steps the work order is closed in the system and all data has been archived for later use.
A Real-World Impact: Improved Efficiency and Customer Satisfaction
The telecom provider in our example has optimized its field service operations by using ServiceMax’s work order management solution. First-time repair rates have increased as a result of the organized method of distributing work orders and the flexibility to alter workflows for various activities. Consumers are happy because their problems are handled promptly and effectively, while the business gains from increased operational effectiveness and lower expenses.
Conclusion
ServiceMax’s work order management system is made to be user-friendly, adaptable, and effective. ServiceMax offers the resources you need to efficiently manage field service operations, regardless of whether your company performs installs, repairs, or preventative maintenance. Understanding the different kinds of work orders and adhering to a defined procedure can help you guarantee that your staff consistently provides excellent customer service, keeping your clients satisfied and your business operating efficiently.
Our telecoms company example shows how using a powerful work order management system like ServiceMax can be a game-changer. Every job is handled with the highest care and precision thanks to the ability to offer thorough documentation, manage parts effectively, and customize workflows to meet unique demands.
Authors: Shivani Kailaswar
2 thoughts on “Field Service Operations with ServiceMax Work Order Management”
Great work!
Amazing work!